Build a house like "building blocks" - the concept of prefabricated housing in Japan
- kaywang6
- Nov 27, 2022
- 5 min read
We can imagine pre-made components such as beams, slabs, columns, walls, etc. as Lego blocks, and only need to assemble them together at the construction site. "Assembly" is not just "building". After the prefabricated components are transported to the construction site, the reinforced concrete will be lapped and poured. This kind of "industrialized" and "industrialized" buildings have been widely used in Europe, America and Japan.
Introduction to prefabricated houses
What is a prefabricated house Prefabricated houses are built by prefabricating some or all of the components of the house in the factory, then transported to the construction site, and assembled through reliable connections.

The difference between prefabricated houses and traditional houses
All the construction of traditional houses must be completed on site, while prefabricated houses can be produced in factories and installed on site.
For example, the balconies, bay windows, and stairs of your home have all become parts of the factory. They are integrated in advance, and when the house is built, they can be directly hung up and spliced together.
Even the floor slabs, columns, and beams are all made in the factory in advance, and only need to be installed on the construction site, but this is more of a test of precision, and there can be no slightest error.
After the prefabricated stairs and exterior walls are transported to the construction site, the reinforced concrete also needs to be lapped, not simply connected. Steel bars run through each structural member such as floor slabs and columns, and the house structure is very strong.

Advantages of prefabricated houses
Prefabricated buildings have the advantages of high construction quality, fast project progress, and environmental protection, so they are very popular.
Japanese prefabricated housing
The History of Prefabricated Housing in Japan
Japan's construction industrialization is gradually developed in the process of meeting the needs of the housing market and continuously improving the quality of housing.
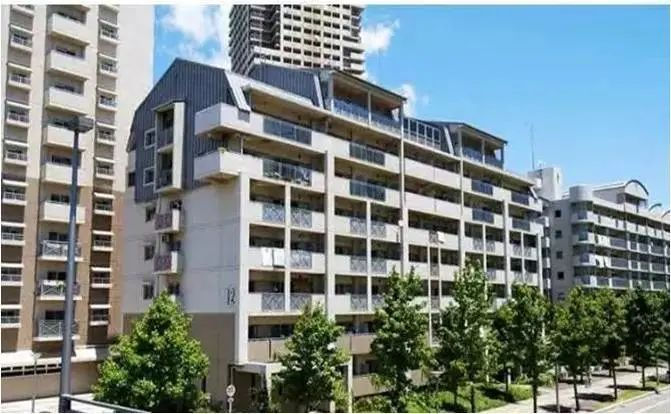
The biggest problem Japan faced after World War II was the housing shortage.
According to incomplete statistics, in the 1940s, there were 4.2 million households lacking housing in Japan, accounting for 1/4 of the population at that time.
In order to solve the "housing shortage" problem, the Japanese government began to use the method of factory production of housing for large-scale housing construction. The housing problem was not alleviated until the early 1960s.
Since then, Japan's housing construction has gradually realized the transformation from "pure pursuit of quantity" to "equal emphasis on quantity and quality" to "multi-faceted comprehensive development", and has achieved rapid development with the strong support of the government.
After nearly 60 years of development, Japan's housing industry has formed a "complete system", and it is one of the countries with the most mature development of housing industrialization.
Classification of prefabricated houses in Japan
Japan divides prefabricated houses into: iron and steel prefabricated houses, modular prefabricated houses, wooden prefabricated houses, and concrete prefabricated houses.
The industrialization of the main structure in Japan is mainly prefabricated concrete PC structure, and a large number of steel structure integrated houses and wooden structure houses are also used in multi-storey houses.
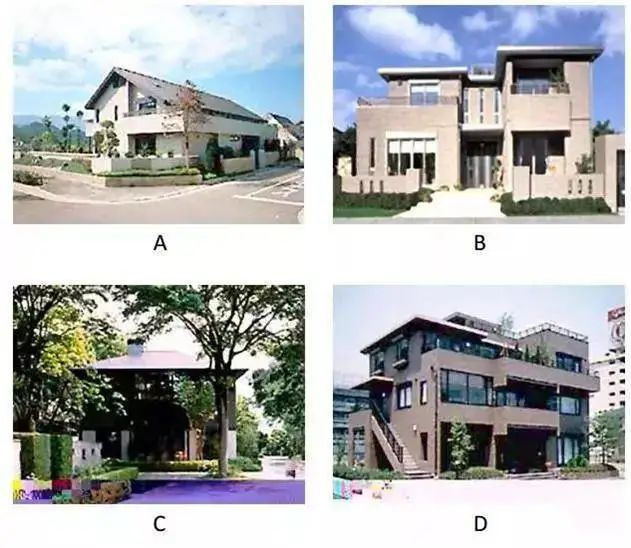
PC structure housing has experienced the development process from WPC (precast concrete wall panel structure) to RPC (precast concrete frame structure), WRPC (precast concrete frame-wall panel structure), HRPC (precast concrete-steel hybrid structure).
Application of prefabricated houses in disaster relief
The Japan Housing Federation built temporary housing for the disaster victims in accordance with the requirements of the governors of each state. Such as the Great Hanshin Earthquake, Mount Usu Volcanic Eruption, and the Great East Japan Earthquake.
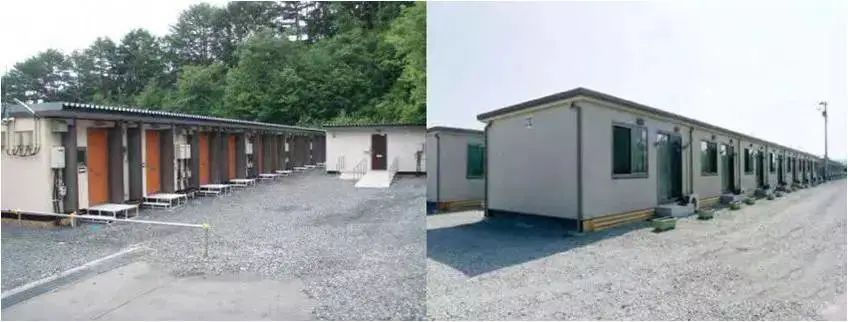
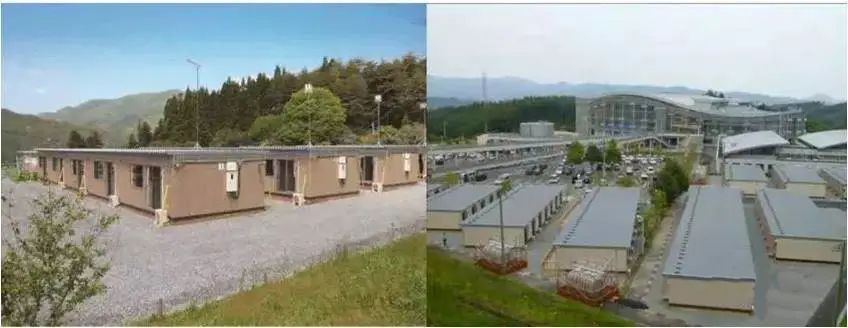
The Japan Housing Federation has signed construction agreements with 47 prefectures in Japan to build temporary housing during disasters. The following table counts the number of disaster relief housing built in each year since 1995.

Prefabricated Building Case in Japan丨Industrialization of Building Main Body
Prefabricated column installation

Prefabricated elements transported to the construction site
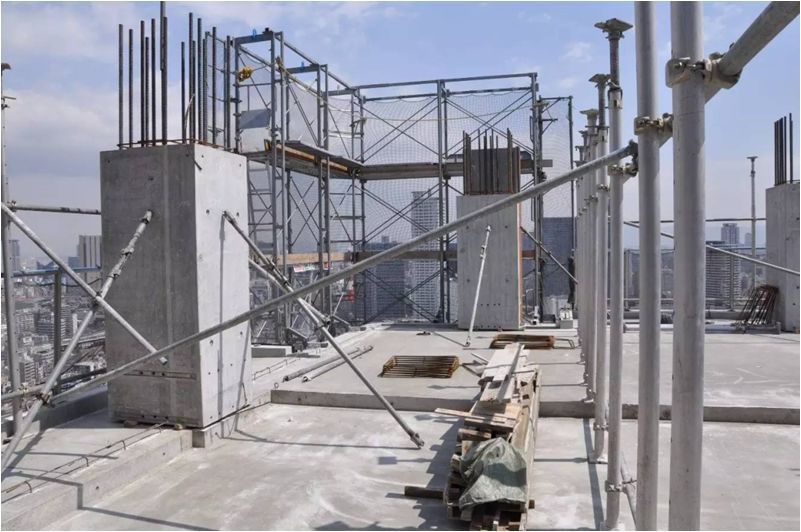
The embedded parts for on-site installation and support have been reserved in the factory in advance
Precast Beam Installation
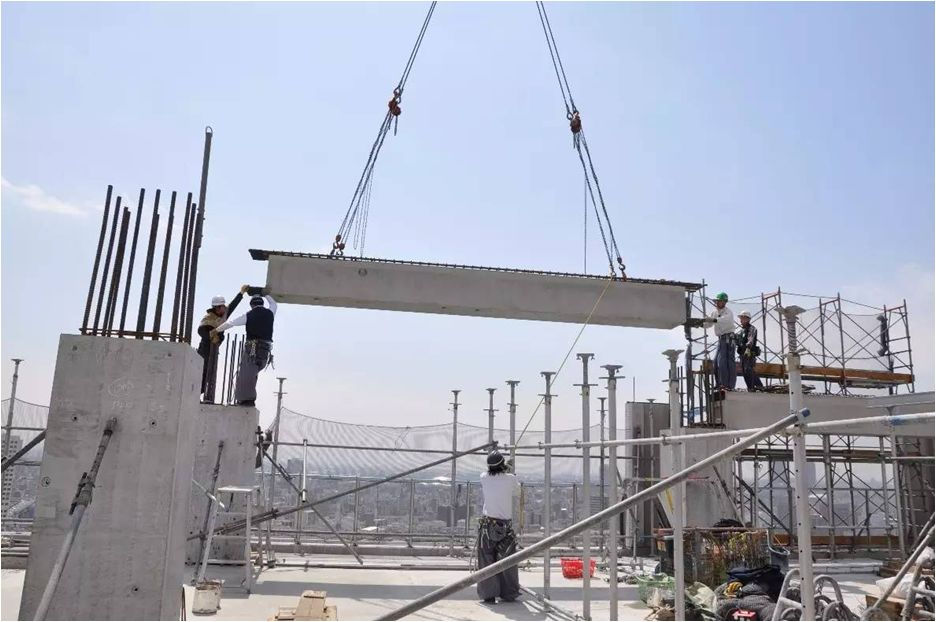
A team of five workers collaborated to install the prefabricated beams

The joints of the prefabricated beam-column components adopt post-cast concrete on site
exterior wall brick

The exterior wall bricks have been completed in the factory along with the prefabricated components. Unlike the customary practice of external wall insulation in China, the exterior wall bricks are directly pasted on the prefabricated concrete components.
Internal insulation
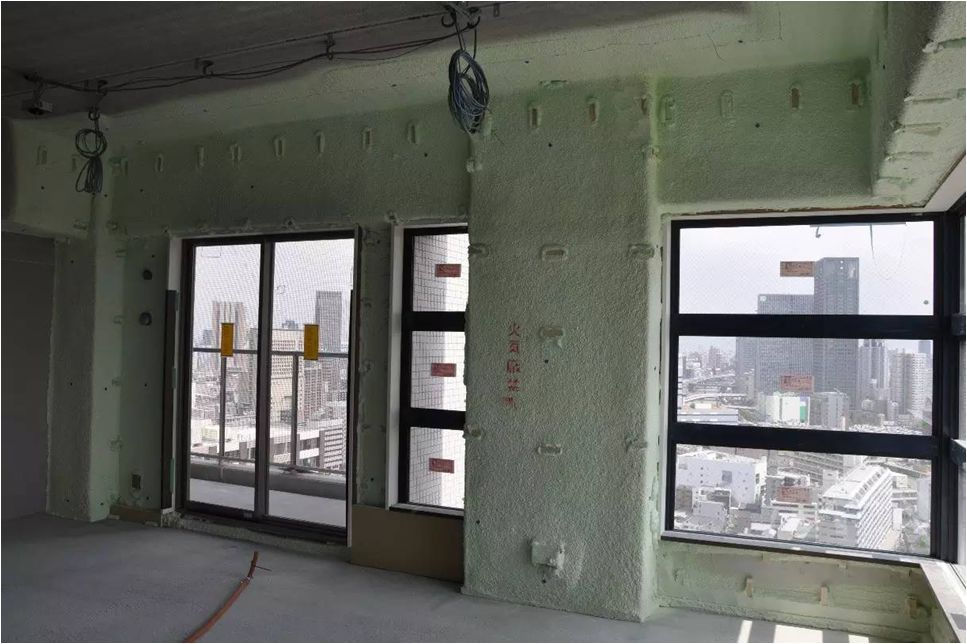
Insulation is done indoors with sprayed styrofoam, which is much easier to construct than the commonly used method of pasting insulation boards on exterior walls in northern my country. You don’t have to worry about the insulation falling off the exterior walls, and it is easy to renew after decades of use.
Seismic Column Node
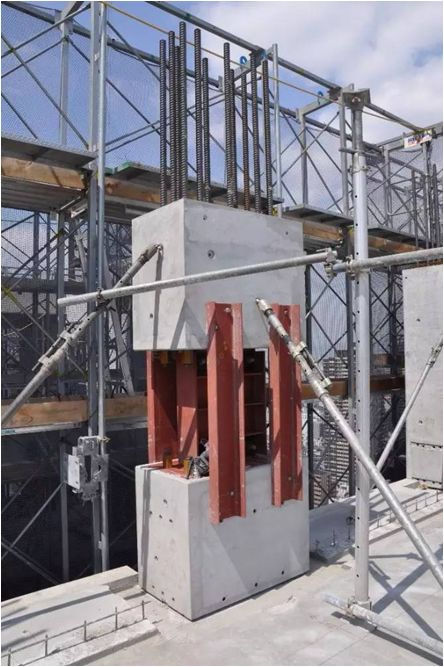
Japan is a country with many earthquakes, and the anti-seismic technology is very advanced. This project is a 50-story prefabricated super high-rise residence, which is the anti-seismic column node.
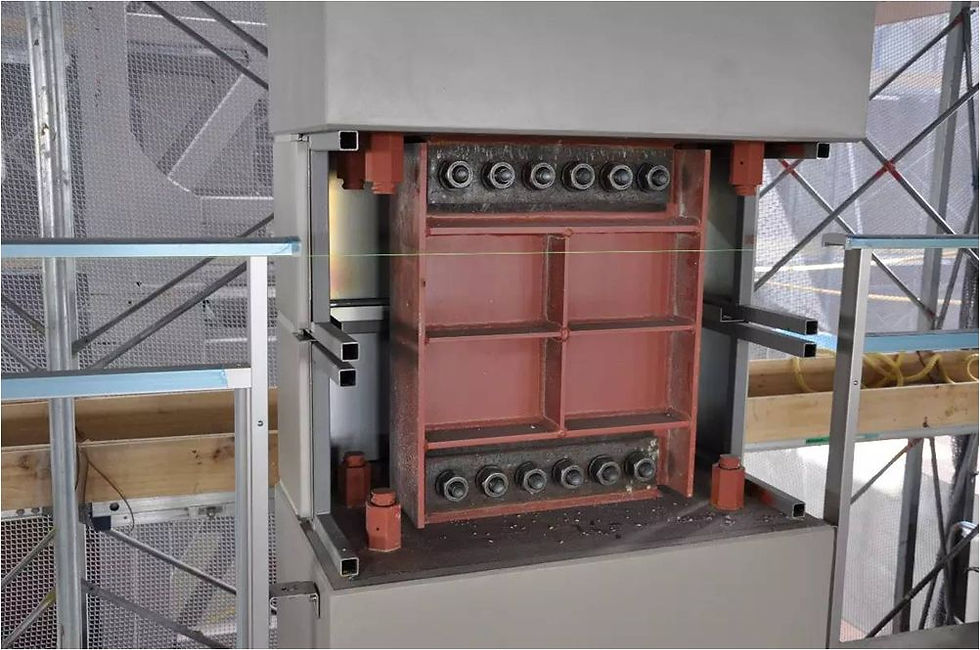
Nodes of installed seismic columns
wall panel

Wall panels transported to the floor ready for installation

Installed balcony wall panels
Japanese prefabricated building case丨Interior industrialization
Construction status of each floor
Each floor carries out a process of construction respectively. The flow line from top to bottom is clear, the processes are closely connected, and there is little mutual interference.
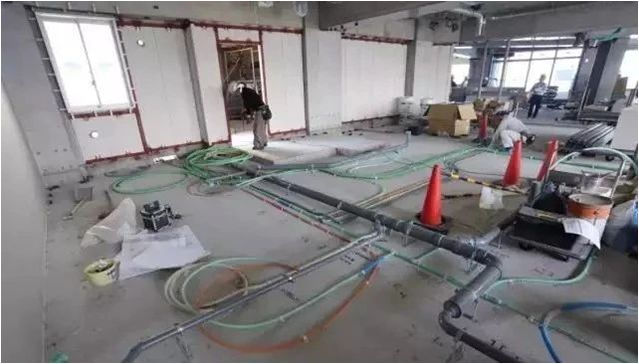
The household wall is completed, and the mechanical and electrical pipelines are installed
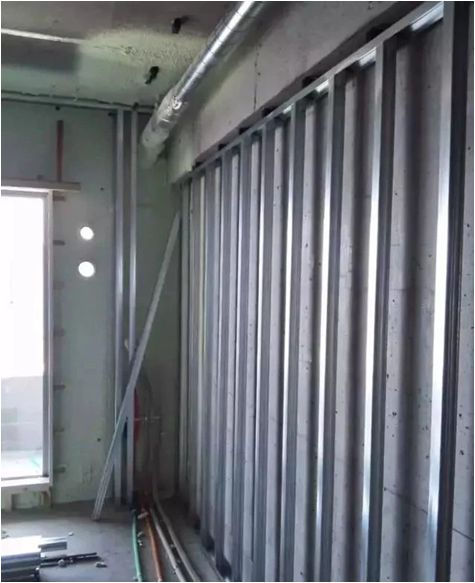
Indoor lightweight partition wall installation, decoration base construction is carried out simultaneously

Decoration keel and detail installation and adjustment, installation of thermal insulation and sound-absorbing rock wool
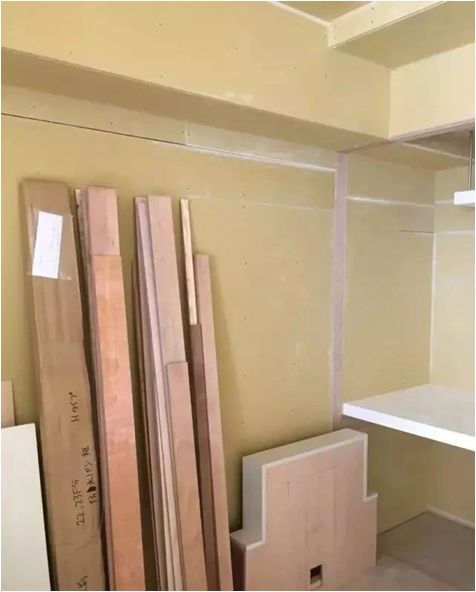
Panel Mounting and Laying of Raised Floors

Interior finishing and overall bathroom installation
Japanese prefabricated building case丨Japanese SI housing and industrialization at the same time
SI (Skeleton-Infill) residence is the name of the housing system proposed by Japan based on the idea of "Open Building (Open Building)" (also known as support theory or SAR theory) by Dutch scholar John N. Habraken. , that is, a collective housing built by a prefabricated construction method in which the building body and the interior are completely separated, which has long-term durability and changeability.
S (Skeleton) refers to the body and public equipment with long-term durability of more than 100 years; I (Infill) refers to the interior decoration and indoor equipment that need to be updated and changed in about 10 to 30 years according to the social and family development conditions.
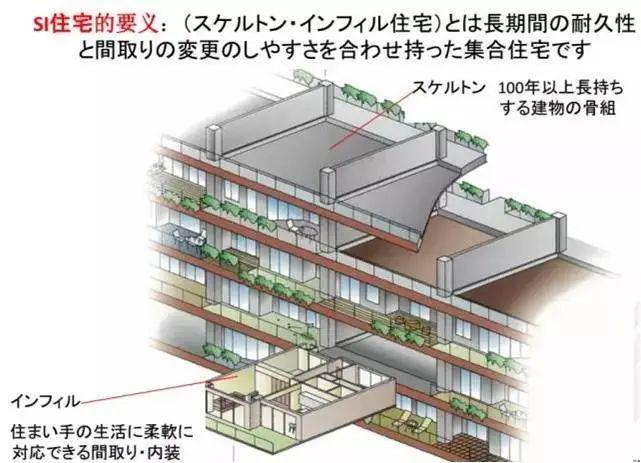
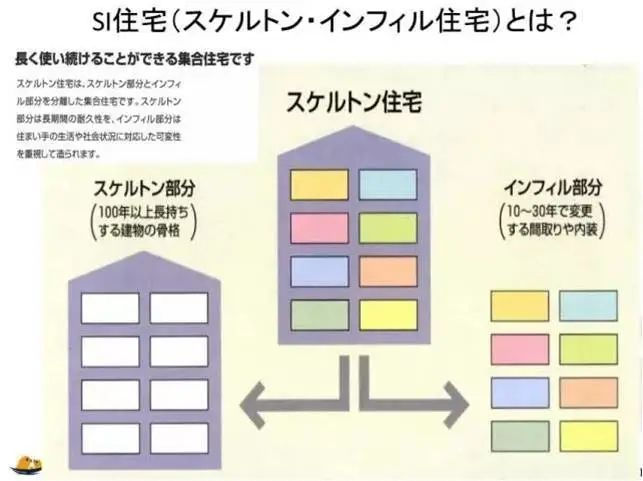
Japan's SI house is an industrialized house, and industrialization runs through all processes. Whether it is the overall building or interior decoration of the house, there is a good operating system.
Firstly, the quality of such a house is well controlled; secondly, for the family, putting the interior products in the factory is to equip all the items to make the room layout and decoration easy to change. Different functions and styles can be designed for different family structures, and houses can be designed according to the principle of the product to achieve more convenient demands of users.
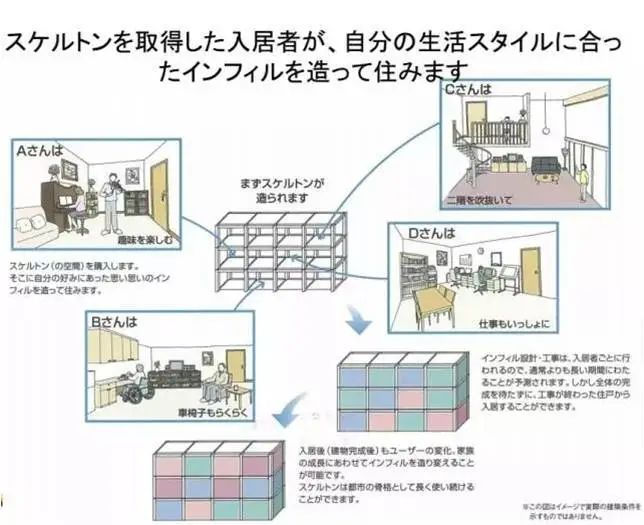
Why Japan's prefabricated building technology is leading
Promote technical standardization of prefabricated building development
Develop prefabricated buildings on a mass scale
About 0.5% of turnover goes to research
Japan's construction industry supports a huge product research and development department. The six most famous construction companies in Japan account for 75% of the country's prefabricated housing. The six largest domestic construction companies are required by law to invest approximately 0.5 percent of their turnover in research and development.
Each of these six companies has billions of dollars in annual net sales and thus has considerable research expenses. Corporate efforts, combined with government funding associations, have made Japan the world's largest base for architectural research.
Japanese "artisan spirit"
Take a large precast factory as an example:
Although the prefab factory produces large-scale components such as prefabricated beams, prefabricated columns, and prefabricated floors, the Japanese are unambiguous about the smallest details, and even the smallest cracks are filled by special personnel.
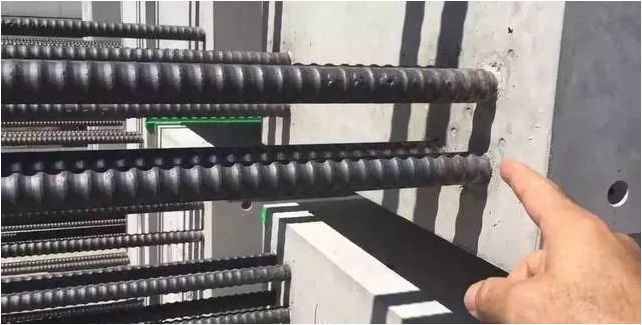

Everyone in the factory has a clear division of labor and clear responsibilities. There are standardized procedures for how to place steel bars and how to transport components, so the work efficiency is very high.


Although this prefab factory has a history of 40 years, the interior looks like a new factory, thanks to the careful maintenance and strict control of the production process by the Japanese.
As far as prefabricated buildings are concerned, China still has a long way to go from Japan. At present, China is vigorously promoting prefabricated houses. It is expected that more Chinese projects will also become the benchmark of technology and quality in the field of prefabricated houses.
Comments